What to expect when designing and developing custom touchscreen display components for your product
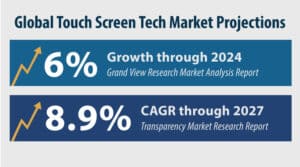
Through 2024, Grand View Research finds, the global touchscreen tech market is projected to grow 6% year over year. Transparency Market Research suggests even greater growth — at 8.9% compound annual growth rate (CAGR).
In simple terms, touchscreen displays are in high demand, which begs the question: Will standard design and development processes garner more market share, or will custom touchscreen display products be in even greater demand?
For product designers, engineers and manufacturers, custom vs standard can mean the difference between a positive, profitable go-live or an unnecessarily lengthy rollout that satisfies few parties — or customers.
Why custom touchscreen display components are often preferable to standard
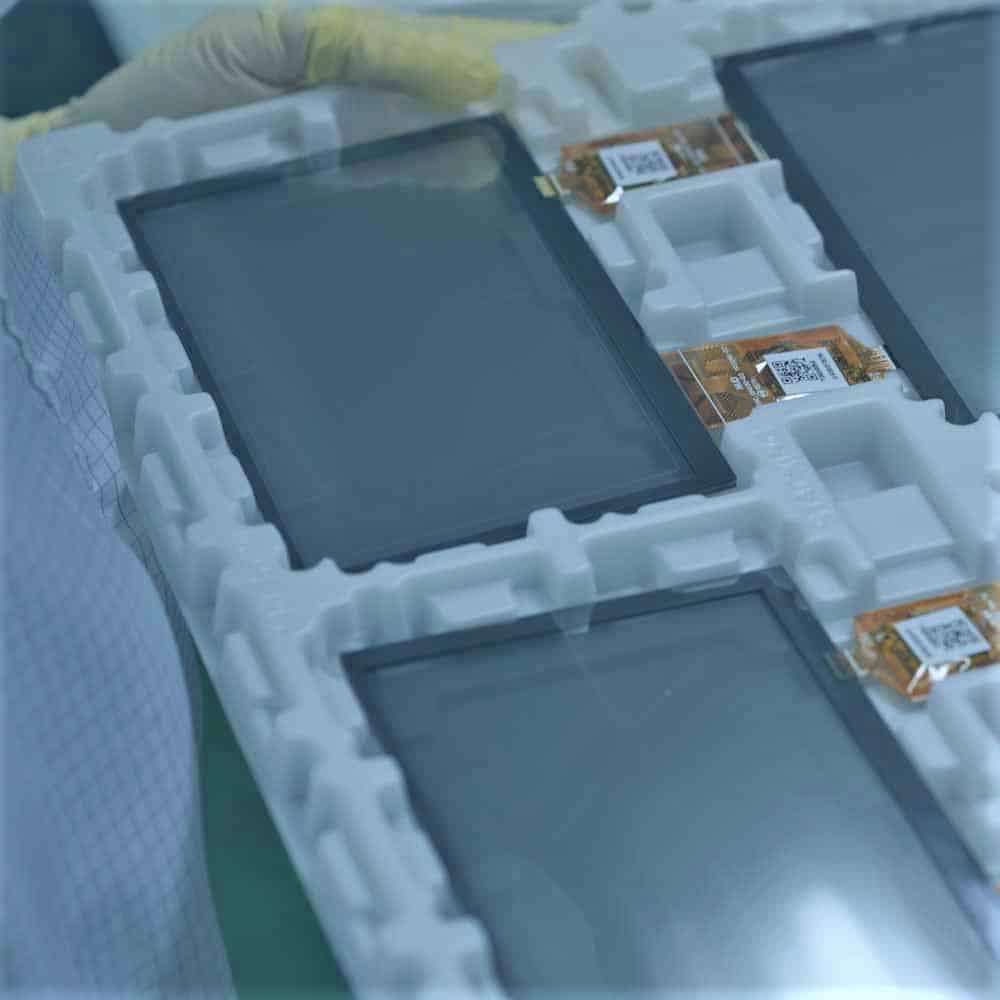
If you’re not 100% satisfied with an off-the-shelf product, then you won’t be satisfied with a standard design and development process.
Even small design tweaks, features and requirements that diverge from a standard setup would best be handled via a custom process. Every add-on and suggestion is feasible — but is best suited for a custom design, so it’s imperative that the goals of the design are clear before concepting begins.
Additionally, custom parts are 100% trackable across the world, meaning the money, expertise and bespoke design you put into the development process are secure between you and the manufacturer.
Lastly, “standard” often implies “cheaper,” but that’s not always the case. Customized touchscreen display products can be designed specifically with cost efficiency in mind, so application-specific implementations can actually generate reduced unit production cost. If you stick with a standard build, you’d be stuck with any standard inefficiencies as well.
The 5-step development process:
At New Vision Display we like to segment our custom product development process into five phases. Here’s a quick walkthrough of what that typically entails:

1. Definition
To start, all stakeholders need to agree on the what, where, why and how. NVD likes to begin with a preliminary questionnaire that covers items like:
- What problem are you trying to solve?
- How does this product solve that problem?
- What is the product, application and timeline you’re working from?
- Why are certain requirements (size, shape, etc.) needed?
During step 1, we’re also evaluating how to best partner with a customer and whether a product is technically or commercially feasible. Then we’ll quote the engagement.
2. Concept
At this stage, we build samples based on tooling orders to justify proof of concept.
3. Design
Once a preliminary quote and proof of concept are approved, we offer a final, formal quote for the project and make a production order for materials required. The custom touchscreen and/or display components are now ready to be fully designed and engineered.
4. Validation
You as the customer validate the efficacy of the custom design, and all parties agree to move into the larger production phase.
5. Production
Beginning with a short-run production of the part(s) and culminating in the final mass-produced version, NVD prepares the quantities necessary for a product launch.
Timeline: From prospect to market
When prospects look for a product development partner, they more often than not have an “idea” of what they want but haven’t fully crystallized the details. They may even have strong preferences on what’s right, but it’s NVD’s job to steer prospects toward what is going to actually work in the end – 1 year, 5 years, 10 years from now.
In addition to the questions during the “Definition” phase, we also clarify:
- Feature specificity.
- Approved vendor portfolio (AVP).
- Production cycle (will your product inevitably be obsolete in X number of years, and how long do you have before you need to go to market?).
It’s always best to be upfront when embarking on a venture like this. If there are clear issues with an RFP, a quote or a design sample, they need to be addressed before moving into subsequent phases of development.
Though there’s a lot of variability when designing and launching custom touchscreen display products, here’s a brief timeline we like to adhere to:

- Week 1: Securing all necessary signatures.
- Week 2-10: First samples are created.
- Week 11-23/29: Mass production, depending on components and complexity. Typically this phase can take 12-18 weeks in its own right.
In total, it can take 3-6 months to get a custom touchscreen display component to market for consumer applications. Industrial or automotive applications might take 1.5-4 years. Products for the medical market can run 3-6 years. Here’s a breakdown of the markets we serve.
These are rough sketches, so please reach out to NVD with actual timelines for your application.
Maintaining timelines and avoiding delays
Regardless of product or application, there are a number of key factors that can either speed up the process or at least avoid extending it, including:
- Padding lead times by a week or two to allow for setbacks, changes or unexpected (but inevitable) delays.
- Conferring on any stakeholder vacation. If all authority runs through individual stakeholders, a vacation can set back development and design by weeks. Factor in disparate time zones around the world, and approvals can grind to a halt. Embed any time off into the quote and production timeline.
- Integrating assembly and design. Securing parts from the same supplier cuts down on vendor management and issues with disparate warranties.
If customers purchase, for example, an LCD and a touch panel from the same supplier, they only have to operate through a single vendor who owns the end-to-end process. This integration makes it much easier to navigate complex product-design timelines without being sucked into the back-and-forth that accompanies multiple suppliers offering multiple answers and introducing multiple vectors for potential delay.
Interested in learning more about the design and development process for custom orders? Contact NVD today to get started.