What are ZBD LCDs?
Adding bistability (image memory) to a display has remained an attractive feature for several reasons. In the 80s and 90s, it was seen as a way to allow displays with a large line count to be realized without the need for an active matrix backplane. More recently, bistability is used in many applications where images are updated infrequently and battery life is important.
Many diverse approaches have been investigated to achieve such operation including, bistable LC (nematic, Cholesteric, Smectic A and ferroelectric), electrophoretic, electrowetting, electrochromic and phase change displays. Only a few examples of these have ever “crossed the chasm” and successfully made it into mass production. One example is the ZBD LCD technology – invented in the 1990s and widely deployed in electronic shelf labels.
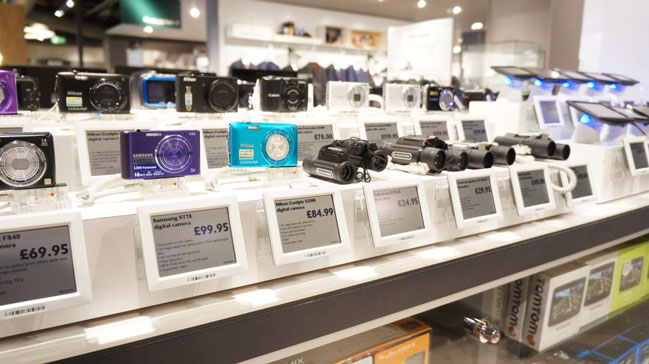
The ZBD LCD technology uses standard nematic liquid crystal materials within a passive matrix display. However, one surface is no longer a rubbed polyimide layer but instead is a microscopic diffraction grating. This interacts mechanically with the long-range order in the LC material and allows two different optical states to be obtained without any holding voltage.
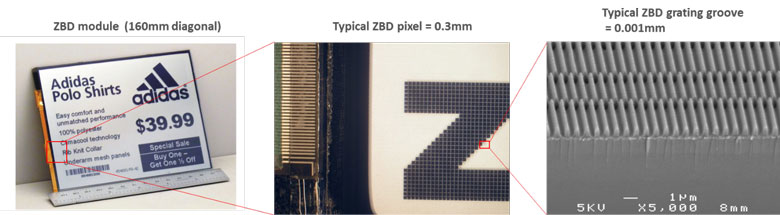
The grating surface is treated in such a way as to force the liquid crystal to lie perpendicular to the local surface direction (homeotropic alignment). This creates a bend and splay distortion in the LC layers within, and close to, the grooves. For an optimum ratio of grating amplitude to grating pitch, there are two very different configurations of the nematic LC near the surface which have the same distortion energy. Crucially, these two configurations impart two very different pre-tilts in the nematic LC above the grating.
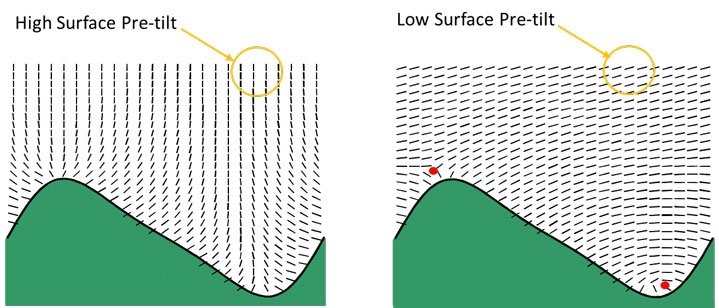
In summary, a microscopic surface grating of optimum dimensions and chemistry provides two stable pretilt angles (typically 90° and 5°) to a neighboring nematic LC. Of course, this is not enough to create a bistable display since we still need a method to switch between the two states. Once again the grating-induced distortion of the nematic provides the answer.
Flexoelectricity is a little-used property of nematic LC materials that arises from the microscopic shape of the LC molecules themselves and leads to a macroscopic polarization within the LC whenever the molecules are subjected to a bend or splay deformation.
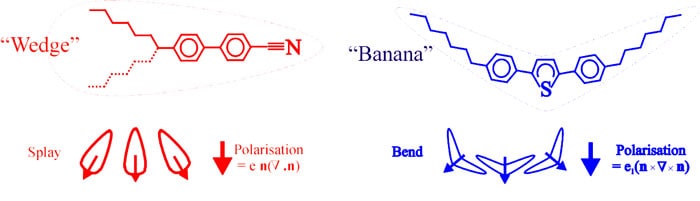
The net polarization is directed towards the grating surface for the high tilt state and away from the surface for the low tilt state. Therefore it is possible to select between the states by selecting the polarity of the applied electrical pulse (in a similar manner to the latching of ferroelectric liquid crystals).
Since there is a distinct energy barrier between the two grating states, there is a well-defined voltage threshold (for any given pulse length) above which a switch will occur between the states and below which the system will simply return to its starting condition. Both bistability and a threshold are required in order to allow passive matrix addressing. This is in contrast to electrophoretics for example where a well-defined threshold is lacking and so an electrical threshold element (TFT backplane) is required instead.
While standard passive matrix STN displays struggle to address more than 256 lines, the threshold behavior in the ZBD LCD allows addressing of many thousands of lines. Indeed, the practical upper limit of display complexity is constrained by electrode resistivity and driver cost rather than the display technology itself.
The biggest challenge in manufacturing the ZBD LCD has been the realization of a cost-effective method of patterning the high-resolution diffraction grating onto the LCD mother-glass. Direct photolithographic methods proved too slow and too expensive. Therefore a replication process was established in which a high-cost photoresist master grating is copied into nickel (similar to CD/DVD nickel stamper tooling) then the nickel pattern is copied into film (similar to hologram fabrication) which is then cheap enough to be used as a consumable surface for the final UV cured replication step onto the LCD glass surface. The replication process speed matches other processes on an STN production line.
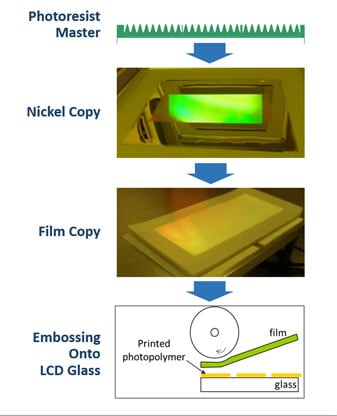
Following the grating replication step, this mother-glass is assembled opposite a standard rubbed polymer surface. This step and all downstream processes use equipment and materials that are common with STN. In the most common ZBD LCD configuration, the grating is placed opposite a rubbed polymer surface such that the low tilt grating state induces a 90° TN arrangement while the high tilt state leads to a HAN (hybrid aligned nematic) arrangement. Usually, front and rear polarizers are arranged so that the TN state is white and the HAN state is black. Unlike a continuously addressed TN display, the bistable TN state in the ZBD LCD has a very low tilt angle throughout the cell and so has much wider optical viewing properties.
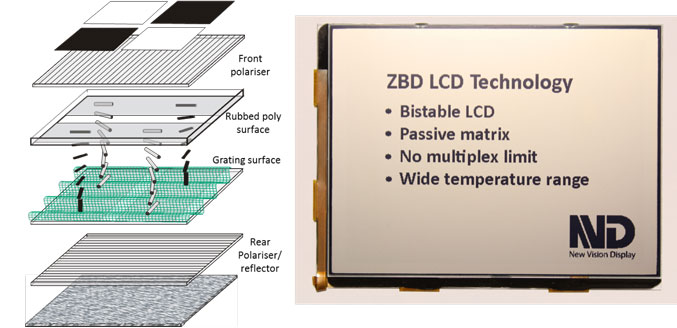
Reflective LCDs have traditionally suffered from a ‘metallic-like’ reflection which means that they only show high reflectivity when the display is oriented close to the specular condition with respect to the user and the light source. In recent years, novel light shaping diffusers have become available which have been used in conjunction with the ZBD LCD configuration to deliver a truly paperlike reflectivity similar to electrophoretic displays.
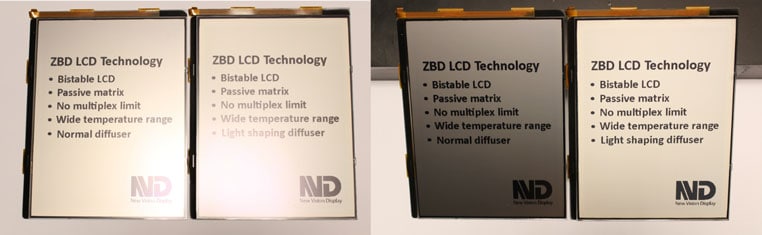
Recent advances in the ZBD LCD technology have also increased the operating temperature range which now extends from -10°C to +90°C. A stored image remains on the display from -40°C to +110°C. Furthermore, these displays can be tested to automotive specifications (e.g. 500 hours at 85°C). These properties together allow a wide variety of portable, outdoor and rugged applications that cannot be served by other technologies.